From Concept to Scale: Optimizing Your Warehouse Automation Strategy
In part 3 of our series, learn how to unlock the full potential of your warehouse automation strategy with expert guidance on design, implementation, and scaling.
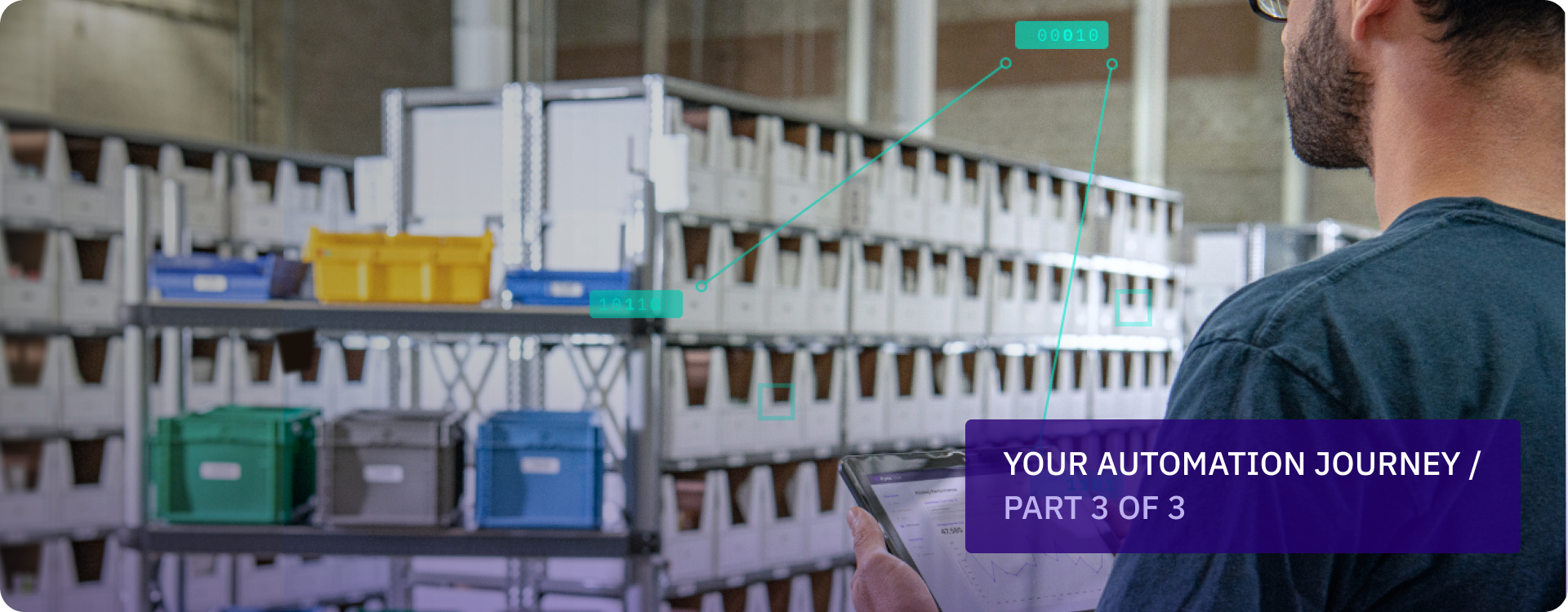
August 15, 2024
With the right automation partner secured, the true work begins—bringing your plan to life. Thoughtful design, seamless implementation, and rigorous validation are pivotal to your success. Expert guidance ensures effective workflows, optimization opportunities, and mitigated risks. Through thorough validation, your new mobile robotic solution integrates flawlessly with your operations.
By partnering with proven experts, you position your company for long-term success—enhancing agility, efficiency, and accuracy from day one.
Step 4: Design and Implementation
Automating manual operations starts with aligning the process design to your desired results. Identifying the right processes to automate for the most impact, simulating and finalizing the design, and integrating with your systems are key milestones to prepare your warehouse for the implementation of an automation solution.
Data Analytics and Operations Modeling
When selecting an automation partner, look for one that is focused on the following:
- Designing automation around your plan: Your plan is the foundation of the automation design. When working together with your automation partner to define the future state of your warehouse operations, start by focusing on the goals of your plan. Are you looking to increase picker productivity, decrease order cycle time, or improve your overall throughput impact? Defining and finalizing your design will depend on your desired outcomes. Reviewing and analyzing your benchmark data to align with your strategy and KPIs are the foundation of automation workflow design.
- Building operational efficiencies: With your operational targets identified, your vendor should evaluate the current process flow and identify impactful changes to support warehouse automation. A detailed analysis of your existing operational data including workflow, resources, outcomes, and benchmarks will help to craft the automation design to target specific processes that will have the most impact. From workstation design to robot routes, a well-designed and efficient workflow ensures each second of material movement counts.
- Simulating and analyzing scenarios: Digitally replicating your warehouse and specific workflows reduces risk and enables proper implementation with fewer errors. Testing various scenarios, such as the ratio of robots to pickers, order volume, and operational hours helps determine the right balance for optimal results. Simulating the impact of robots on the operational process and in the warehouse saves cost and time without experimentation on the floor during valuable peak hours.
Design Recommendation and System Integration
The final stages of partnering with an automation provider involve customization and integration. The right partner will recommend a design tailored to your process and criteria. After completing scenario testing, they’ll provide a final design and fleet size recommendation. They’ll demonstrate anticipated ROI and output targets, identifying targets for both typical and peak volume scenarios. Together, you’ll review and align on a detailed outline of the proposed process, including robot and people requirements.
Integrating with your existing warehouse systems is the next crucial step. Between design and implementation, your partner will define system workflows and requirements to support integration with your WMS. They’ll work with your onsite IT support to ensure proper integration. Once WMS integration is defined, developed, and tested, onsite implementation can begin.
The Roadmap to Successful Automation Implementation
When planning is complete, your robots and onsite vendor support arrive, marking the start of the implementation phase. This stage involves deploying and integrating autonomous mobile robots in your warehouse. It ensures seamless communication and coordination across the robotic fleet, existing infrastructure, and human workers. Testing and optimization of processes are conducted to validate the effectiveness of the mobile robotic system in real-world scenarios. Throughout the implementation, close monitoring and modifications are made to establish a smooth transition and quickly address any unforeseen challenges.
Components of a Successful Implementation
When choosing your automation partner, consider these key components of successful implementation:
- Understanding the environment: Mapping the warehouse provides valuable input into what robots can or cannot do within the work area. Capturing detailed information about the dynamic warehouse environment allows both robots and humans to navigate efficiently.
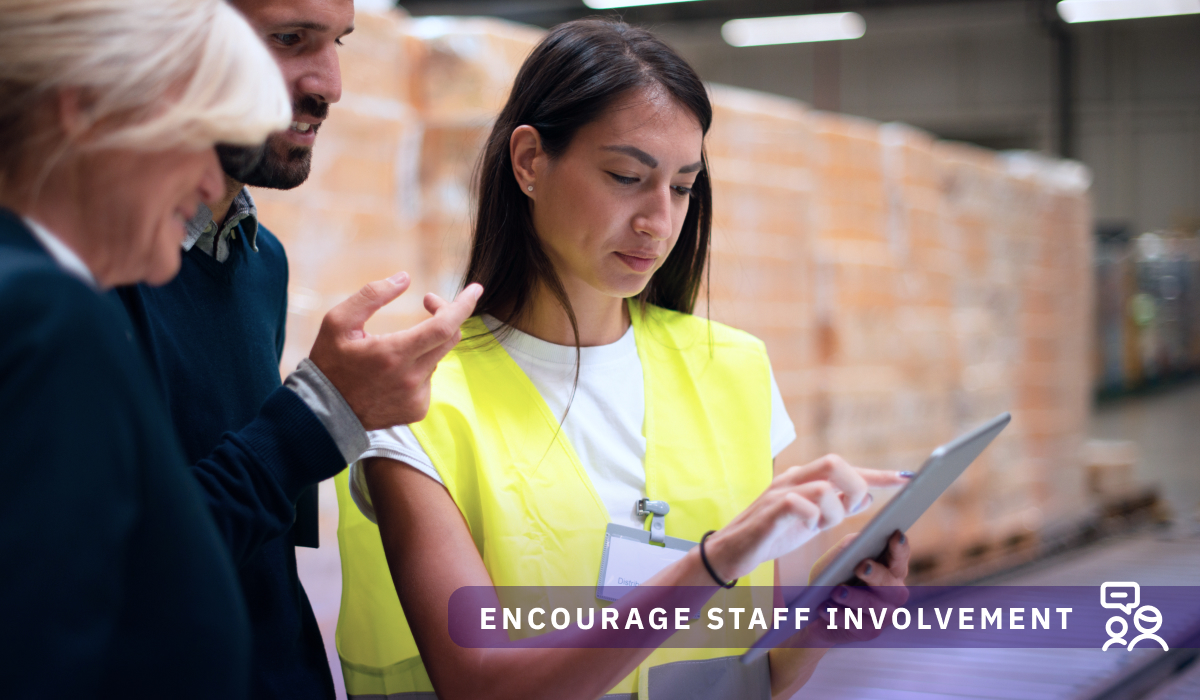
- Onboarding to enable buy-in and success: Employee knowledge and adoption of automation are crucial to achieving your automation goals. Effective training, follow-up, and support from your staff ensures they are prepared and comfortable working alongside robots and with the new workflow. Encouraging active participation increases acceptance and promotes ongoing use.
- Ensuring digital and physical integration with operational systems: Confirming proper function and communication with both physical and digital assets confirms operational readiness for warehouse deployment.
Implementation of mobile robotic automation in your warehouse is gated by achieving the success criteria agreed upon with your automation partner. Successful automation implementation should meet your acceptance criteria, with demonstrated outcomes prior to going live. However, vendor support should not end there.
Ongoing support and a proactive approach from the customer success team are essential. They should monitor and analyze user, robot, and process data to identify opportunities for improvement and expansion, making course corrections as needed. Your support team should possess an in-depth understanding of your warehouse and processes as well as you do. This alignment is crucial for maximizing utilization, assisting you in reaching your targets, and providing the necessary information to enable enhanced decision-making.
Step 5: Measure and Scale
Successful design and implementation demonstrate not only the functionality but also the operational impact of automation, enhancing operational efficiency, productivity, and throughput. After implementation, tracking key performance indicators helps continuously improve processes, demonstrate ROI, and adapt to evolving demands. Automation should support and enable your business as it continues to grow and evolve–providing the flexibility to scale your fleet and expand to other processes and facilities.
Measuring Success
The definition of success–as agreed upon in design and achieved in implementation–should be monitored and updated as needed to evolve with changes in demand or your processes. Measuring progress provides data-driven insights that empower decision makers to make informed choices regarding adjustments, improvements, or investments in additional automation.
When measuring success, it’s common to track things like:
- Throughput
- Availability of robots and pickers
- SLA delivery criteria
- Cycle times
- Error rates
Proactive Monitoring of Benchmarks
Ongoing measurements and data analysis will ensure your investment delivers on your commitment to the business. Enterprise software should support your daily management with real-time performance and progress insights, offering up-to-date views on your team’s productivity. This data should provide a day-to-day snapshot of what’s been completed, what’s in progress, and what needs your attention, including throughput, work orders in queue, work orders waiting to be finished, what is in the “hospital,” and how many orders are short.

For example, by actively monitoring your robot utilization rate, your partner can recommend adding to the fleet to ensure business continuity. With automation powered by technology such as Onward Robotics’ Pyxis technology, your partner can provide not only robot but picker data analysis, suggesting opportunities for improved efficiency, reduced travel time, and sharing picker best practices. This unique feedback, part of Onward’s Meet Me® model, optimizes your human and robotic team with measurable outcomes to make your most valuable resources work better together.
Onsite visits and follow-up are also essential—even when operations are running as expected—ensuring that your automation partner is updated on not only performance but also changes that could impact outcomes such as warehouse layout, process updates, or reallocation of resources. This ongoing data reporting, analysis, and communication is key to ongoing automation success and growth.
Scaling for Continued Growth
From learning, adoption, and success to scaling automation in your warehouse and beyond, your automation partner should also be your advocate: identifying additional workflows or sites within your network where your fleet and business can grow. Demonstrating success will help to build your confidence and the business case for expansion. With initial process implementation and ongoing success, you can add to your fleet or leverage your existing robots, reassigning them to other processes or facilities by repeating the design and implementation process as needed.
Whether expanding your fleet further into your network or scaling for peak season, your vendor should provide purchase options that align to your business needs—capital purchase or RaaS options can provide the ability to scale up or down as demand fluctuates. Integrating automation across your operations positions your business as technologically advanced and efficient, giving you a competitive edge in a rapidly evolving market.
An Ongoing Journey
Each step of the automation journey is essential to realizing operational outcomes that move your business forward. Achieving your initial automation plan goals is just the beginning. Warehouse mobile robotic automation provides the opportunity to optimize resources, reduce costs, increase productivity, and provide the flexibility needed to adapt when talent is scarce, resources are tight, and customer expectations are high.
Automated workflows not only boost efficiency but also contribute to cost savings, error reduction, and improved adaptability to dynamic market demands, positioning the warehouse for heightened competitiveness in the modern business landscape. Following these key steps at each stage of your automation journey will grow your business as well as customer satisfaction—improving accuracy, efficiency, and adaptability.
Automating With Onward
Fulfillment warehouses face growing pressure to boost capacity and flexibility while optimizing resources. Onward Robotics’ innovative Meet Me solution provides the efficiency boost needed to stay competitive. As a true automation partner, we propel your business forward with our powerful person-to-goods solution. By reimagining how robots and humans work better individually and as a team, Pyxis technology empowers and augments the human workforce and streamlines end-to-end operations. Contact us today.
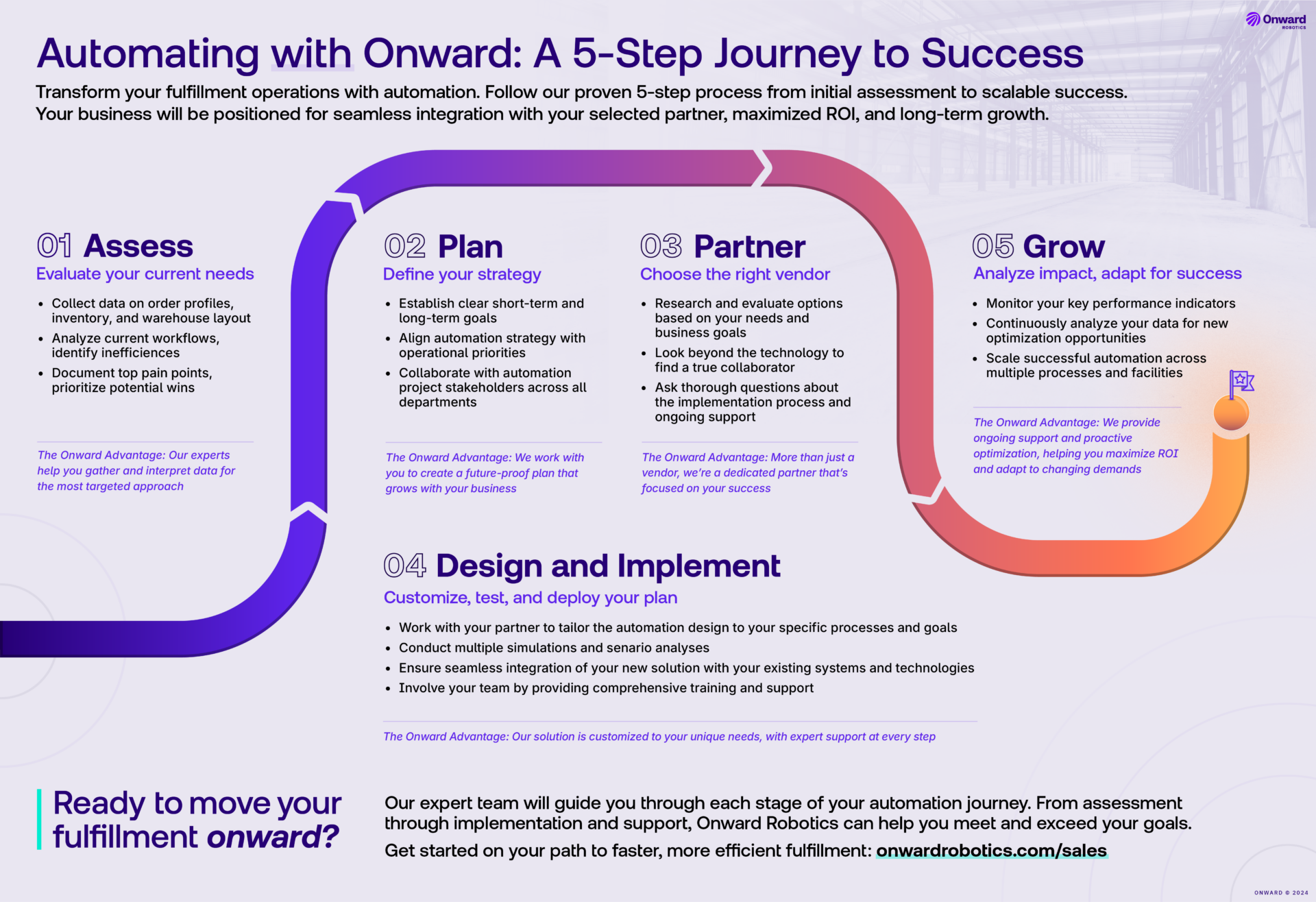